

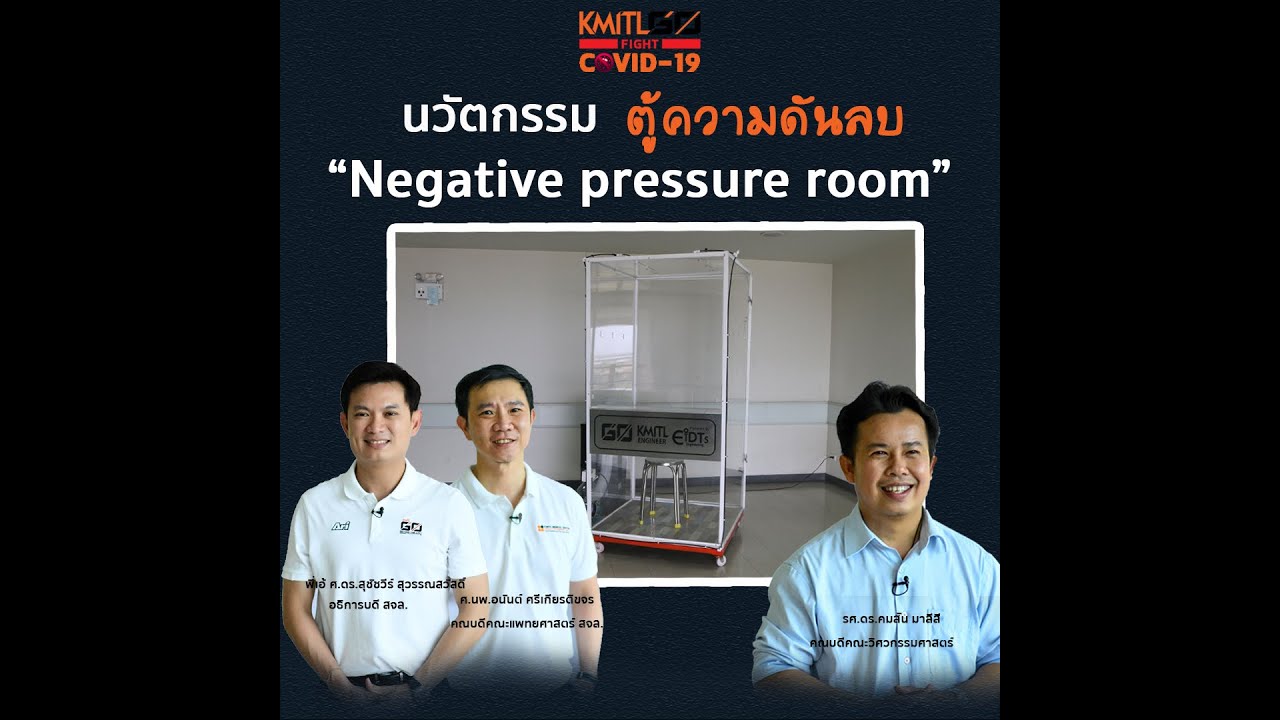
As an example, computers feature small fans to blow out debris and dust to avoid build up and product failure, while smaller component manufacturers such as those making PCB boards and other computer chips will benefit from positive pressure room to ensure that the newly manufactured parts are not defective from new. Positive air pressure can be applied to both cleanrooms and within finished product, ensuring contaminants and dust don’t affect the product performance. Positive air pressure rooms are common in hospital environments such as human and animal nurseries, vitro fertilisation labs and operating theatres. In medical settings, positive pressure rooms are referred to as protective environments. Positive pressure rooms maintain a high pressure inside the treated area by constantly pushing old air out and in scenarios that must continually filter harmful contaminants out of the environment. Any contaminants are forced out of the room with the old air, ensuring a clean air supply. The supply fan, also known as the intake fan, replaces the old air with freshly pulled in filtered air. In a positive air environment, the positive air pressure pushes air out of a room by increasing the airflow rate. Usually in multipurpose rooms indication lights on a control panel or display can show the airflow direction status whether positive or negative. In multipurpose rooms, a well designed ventilation system can switch the flow from positive to negative, and vice versa, depending on the nature of the work being performed. Maintaining positive or negative air pressure is an important metric in cleanrooms located in hospitals, labs and other manufacturing facilities, ensuring a clean, non contaminated air supply.
